Flexible and mono-material packaging, the solution for achieving the circular economy
The European Union, since 2015, is fully committed to achieving climate neutrality by 2050. Throughout these years, a set of initiatives have been promoted that affect all sectors and industries. One of the main goals is to make all packaging reusable or cost-effectively recyclable by 2030.
It is clear that, in this case, regardless of the sector, the packaging industry must make changes that will affect both producers and consumers. The packaging industry must achieve a circular economy that allows the reuse of packaging in the most efficient and durable way possible.
The circular economy is the solution. But what is the circular economy?
Focused on recycling and its role in the permanence of materials within the production cycle, based on the fact that the entire cycle must be weighed and thought for the reintroduction of the material in the flow of materials. It is a complicated but achievable goal, based on this: where are we today? What are the objectives within the packaging industry? How are we running the race to achieve the goals in 2030?
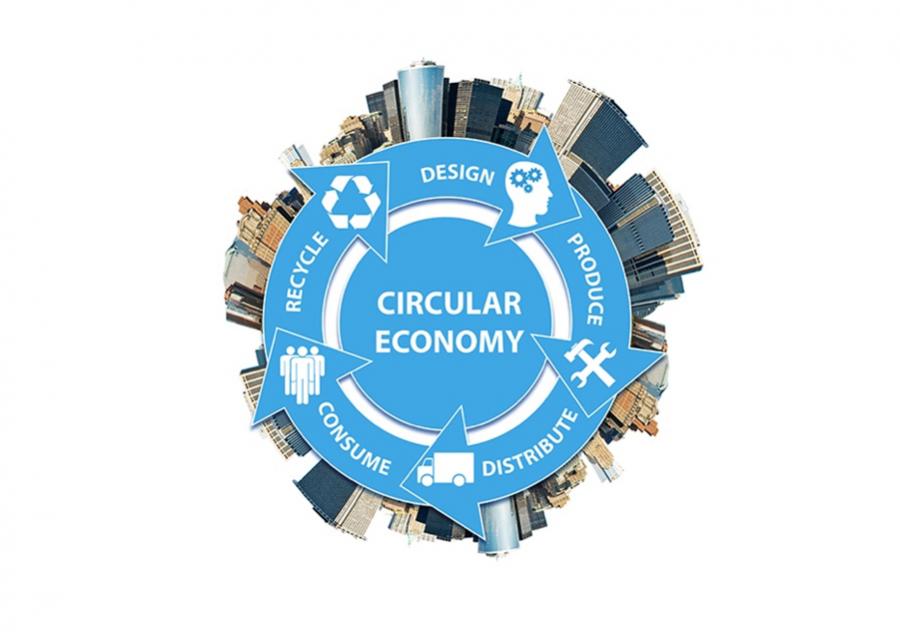
We can proudly say that the world of packaging is evolving to find a balance between shelf life, product safety, and environmental impact. Eco-design, the use of mono-materials, post-consumer recycling, and educating consumers on the separation of plastic waste are some of the trends towards which the sector is heading.
Bringing together all the actions mentioned, with an investment in R&D and many hours of work since 2015, the world of packaging has made a very important qualitative and quantitative leap. Considering the use and recycling of different types of polymers, including PP, PET, HDPE, and PE as the main tool to combat waste and gradually approach the 2030 goals. Placing ourselves in the current framework, in 2015, in the case of flexible polyethylene (PE), we were recycling 1.5 million tons per year in the EU. We can proudly say that we are currently recycling 2.3 million tons per year. Despite achieving a significant qualitative and quantitative leap, we are far from optimal objectives. The European plastics industry has an extrusion capacity of 7.4 million tons of flexible PE, which means that we have a current recycling rate of PE of 31%.
There are currently five countries that stand out in terms of installed PE recycling capacity: Spain in the lead with 18%, followed by Germany (17%), Italy (13%), Poland (10%), and finally, France (6%). And as for the production of polyethylene waste, the main sources are shops and distributors (43%), followed by production waste (23%), agriculture (17%), and domestic packaging (13%).
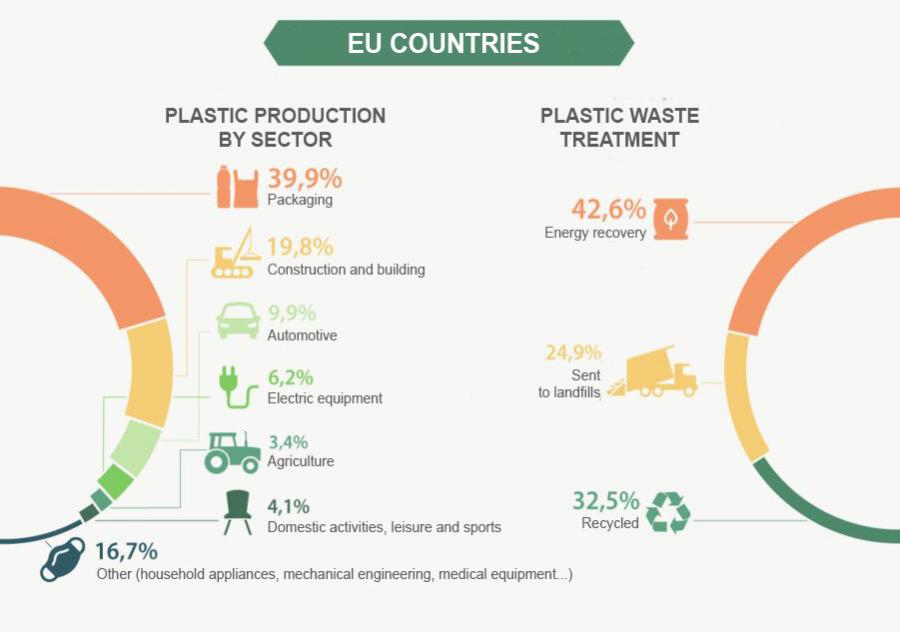
The data speaks for itself, and after numerous studies, the results obtained are clear and concise: one of the main ways to reach 2030 and meet the objectives set is to promote flexible packaging made of a single material, or as we currently call it: mono-material packaging.
On the one hand, the benefits of flexible packaging for both manufacturers and consumers are significant. Flexible packaging protects the quality and integrity of the package contents while offering unparalleled functionality. Furthermore, compared to rigid packaging alternatives such as glass and metal, flexible packaging demonstrates better performance when it comes to sustainability parameters such as reducing carbon footprint. In addition, flexible packaging provides cheaper and more ecological logistics, especially when compared to rigid packaging. In the case of rigid packaging, more air is transported, which occupies more volume and reduces efficiency. In short, the transported volume/kg ratio is very low in flexible, so for the same number of transported kg, there are many more potential containers than in rigid, and therefore there is much less contamination.
Adding the advantages of flexible packaging, the optimum would be for it to be made of mono-materials since they improve the recycling capacity. Mono-materials are a revolutionary ecological and logical evolution in the packaging industry. The method is surprisingly simple: the choice of a single ecological mono-material (such as PP, PE, and PET) allows selective sorting and optimal recycling. After recycling, they begin a second life as flexible packaging (if they are not flexible in their first life). This process, unlike other types of packaging, allows recycling to be repeated in an ecological way in the long term.
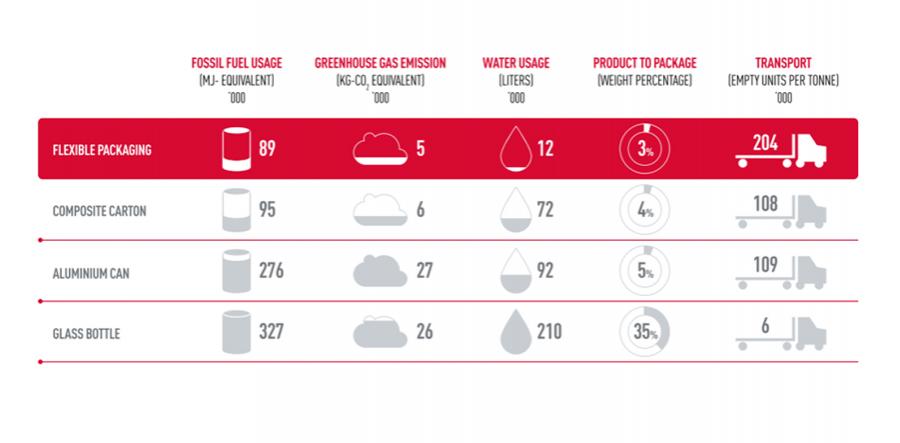
In addition to the ease of recycling, mono-materials have many advantages that we must highlight:
- Allows you to create a single process.
- Simplifies the packaging process.
- Lower consumption of energy and resources in its manufacturing process.
- Cost reduction, because by making containers with a single material, the production process is simplified.
- Protects the quality and integrity of the contents of the package.
- Aesthetically pleasing.
- Flexible in every sense of the word and therefore suitable for multi-sided printing, lamination, and efficient transport.
- Reduces the need for new resources.
- Facilitates selective separation for producers and consumers.
- Facilitates complete recycling without added costs.
- The recycling chain is streamlined and costs are reduced.
- Increase the recycling fee.
From Volpak, we can say that our extensive presence in the global market and our close cooperation with key players in the FMCG segments around the world provide us with extensive knowledge and a lot of information about the needs of not only our customers but of the general market needs in the packaging industry.
We invest 5% of our income in R&D. This investment, made year after year, has allowed us to improve our products and develop new innovative solutions that adapt to the new needs not only of our customers but also of the market.
As we have mentioned, the packaging industry is not excluded from the need to improve its sustainability ratios and reduce the waste generated. At Volpak, and thanks to the efforts and resources dedicated to the R&D department, we have made our machines stand out for their energy-efficient production and maximum versatility in managing different types of film, including recyclable ones, thanks to their unique and innovative features.
Suppliers, producers, and consumers are in a marathon of vital importance. Failure and delay are not options. It is up to all of us to leave a mark and change the negative trajectory towards a green and healthy world that future generations can be proud of.
All our flexible packaging solutions are ready to work with mono-material plastics. You can take a look at them here.