A closer look at the pouch-filling process
A lot can happen in 400 milliseconds: in the case of horizontal form fill and seal (HFFS) pouching machines, the whole high-precision process of filling pouches has to happen within this very short time frame.
The key is to have a strong knowledge of the product in order to be able to control its flow into the pouch with the most precise dosing accuracy possible. Different parameters need to be taken into consideration to define the correct filling technology and obtain the best results.
As experts of their own product, the brand owners’ need to share their product knowledge with machines manufacturers, the more the machine manufacturer knows about the product, the more likely they can ensure the correct technology choice, a consistent flow characteristics and accurate dosing for the brand owner’s product.
When it comes to powdery products, many different properties work together to influence which type of dosing machine is required as well as its performance. These range from granulometry and uniformity of grain size, all the way to fluidity, density, and hygroscopic properties.
How dosing accuracy works
Most commonly, powders are dosed using an auger filler, which is a dispenser that continually releases a pre-set volume of product. The dosage can be controlled electronically by adjusting the precise number of times the auger screw turns per cycle. Due to the fact that these type of fillers measure the quantity of product per dose by volume and not by weight, the granular parameters therefore affect the accuracy of filling.
To achieve accuracy, the first rule is to ensure you are working within a stable environment. In other words, it is important to ensure there is a continually stable quantity of product in the “hopper” of the dosing equipment, which is the name of the cone-shaped container that holds granular and powdered materials. The feeding system synchronizes with the auger filler thanks to special detectors that are able to measure the level of product being held inside.
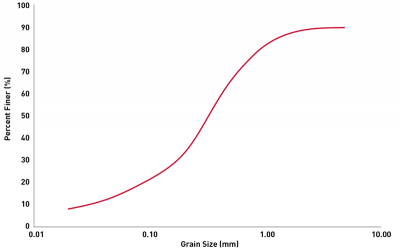
Powders are made up of many different particles. The distribution of the size of the particles is represented in a warhead curve and influences the dosing precision: the narrower this curve is the greater the precision that can be expected.
The size of the particles are important for product quality as well. The product stirrer, the auger tooling, the interference of the screw, and the tube need to be designed to ensure no breakage of the particles.
Powder fluidity and hygroscopy
Another very important characteristic is powder fluidity. This is what will determine the ability of the continuous dispenser to prevent product leakage between doses. This characteristic is valued through the angle of repose, which is slope angle that forms product when dropped on a flat surface. The smaller the angle, the greater the flow is, so the retention system to prevent leakages between doses has to be more obstructive.
Environmental conditions also influence the dosage: take hygroscopic products, meaning compounds that attract water in the form of steam, for instance. The behavior of these products changes according to the humidity level and have a tendency to become compact, thus altering the quantity of product that is dosed in each cycle.
Overall, these aspects of dosage and flow in the filling procedure are essential. The more you know about the internal workings of your HFFS machine’s filling process, the more likely you will be able to autonomously identify any potential issues before they happen.
At Volpak, we are always ready to share our knowledge in order to support our customers’ prevention of mishaps during the filling process. In order to find out more, contact us using the information below.